Editor’s note: The story below is based on a presentation given at the recent PCT Termite Summit in Houston. Look for additional stories from the summit in future issues of PCT.
Ask any room of PCOs what the No. 1 industry liability is and I bet they will respond in unison, "wood-destroying insect work." These liabilities can be related to inspections or treatments; however, the majority of liability claims stem from wood-destroying insect or, in some states that require it, organism inspections for real estate transfer. As there is minimal litigation related to wood-destroying insects other than subterranean termites as a comparison, this article will focus on subterranean termites and will use the term "WDI" since the majority of states only require inspection for wood-destroying insects.
Many companies have shied away from the business of WDI inspections due to past history of litigation or because they want to focus on other business opportunities which have lower liability. Insurance companies also are becoming picky; the risk of non-renewal by the company is real if there are unacceptable levels of claims. Industry insurers report that wood-destroying insect work accounts for 75 percent of insurance claims against our industry and 93 percent of those claims are inspection related. By taking a few simple steps, liability can be greatly reduced, allowing companies to aggressively pursue WDI inspections and gain new customers due to treatments or by adding pest control services to that account.
SETTING THE RECORD STRAIGHT. There are some easy tips to ensure that liability is reduced. A few of these are:
• Be detailed on the reports. Nobody has ever lost a suit because they performed a good inspection by examining all critical areas, and gave an accurate and detailed report. Agreed, lawyers will take cases and sue even if you did a good job, but there is no reason to think that being vague will help. Quite the opposite is true in that if you have vague details and no other information, you weaken your defense.
• Use disclaimers carefully. Disclaimers should be fair disclosures of what is performed and what is not performed in exchange for a fee. Even if a company doesn’t collect a fee, the terms and details of that report are still a legal document. Claiming that the report is void if a fee is not collected is not a valid disclaimer. Since, according to attorneys, the report form is really a contract, disclosures can be added but they must be fair and reasonable in the eyes of the court.
• Make sure that probing, sounding, moisture readings and use of safety equipment are part of the process. Disclosures, industry practices, proper training, and experienced inspectors are irrelevant if a thorough inspection is not conducted — this includes probing and sounding and also the use of a moisture meter in many situations. Some states have regulations that require probing, sounding and even the use of moisture meters. There are countless new tools available from acoustic detectors to remote cameras to infrared detectors, but they are not yet part of the standard practice in conducting inspections.
However, it is not possible to defend an inspection where probing, sounding and (if necessary) moisture meters were not used. A probing and sounding tool called the Probemaster (phone: 203/468-1444) was developed by an industry inspector and is perhaps the only such tool developed exclusively for inspections. Moisture meters have changed dramatically since the "pin" type of moisture meter. Since "pad"-type moisture meters can read behind brick, drywall, and even concrete, these tools will help zero in on potential moisture spots. Proper clothing, leather gloves, a flashlight, and knee pads ensure that the inspector can get into dirty or tight areas.
DOWN AND DIRTY. An informal survey conducted by the author in North Carolina (where most houses had crawlspaces), showed that for inspections where evidence of wood-destroying insects was found, 89 percent of those inspections found evidence on the exterior, in the basement, or in the crawl. Ten percent of the inspections found evidence in the garage or interior, while 1 percent of the inspections revealed evidence in the attic. (See chart at left.)
This clearly demonstrates the importance of performing a thorough inspection of not just the exterior and basement or crawl but of the interior as well. According to the survey, if there is evidence of infestation and the inspector does not go into the garage and attic, evidence will be missed in more than one in ten inspections. It is tempting to take some shortcuts with inspections when the customer is not present, but that risk is just not worth taking. If any area is obstructed or inaccessible, it can be reported as such and not entered, thus protecting the inspector and reducing the liability of the company.
A SYSTEMATIC APPROACH. Now that all of the necessary preparations and procedures are in place for inspections, there are a few specific final tips that should be implemented. These go without saying but they do merit mentioning.
• Start outside; work towards inside and change pattern from time to time. As the survey shows, most evidence of wood-destroying insects will be found outside or in the basement or crawl. A thorough inspection of these areas will have the greatest chances of finding evidence of WDIs. It is good to alter your work pattern from time to time so that rather than left to right, the inspector goes right to left. Studies have shown that human nature is to be more observant if a regular pattern is not established. Directions must be noted in the file so "left and right" describe areas as you face the front door.
• Keep notes and fill out each report as if you will be defending it in court. All observations should be carefully recorded and maintained. Some companies have a "field worksheet" for this purpose so that notes can be reviewed before the report is issued. Reduced errors occur when the final report is completed as soon as possible after the inspection. The notes should be detailed so that the next time that they are read there is no question as to observations or details.
• Perform spot checks or quality assurance; support education. Owners and managers should reinspect the house after the inspector has finished from time to time to check on quality and make sure that the inspector meets the company’s requirements for inspections and reporting. Also, some state associations (Nebraska, Maryland, New Jersey, Pennsylvania, Virginia, Ohio and North Carolina) have developed accreditation programs for inspectors. These are all excellent and should be supported. Most also will accept out-of-state inspectors to the courses.
CONCLUSION. Be careful when performing and reporting on wood-destroying insect inspections. Using these suggestions will significantly reduce liability associated with wood-destroying insect inspections.
The author is technical director for the National Pest Management Association. He can be reached via e-mail at gbaumann@pctonline.com.
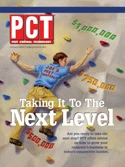
Explore the January 2004 Issue
Check out more from this issue and find your next story to read.
Latest from Pest Control Technology
- Webinar: Maximizing Cash Flow — Key Strategies for Business Growth
- WorkWave Announces Wavelytics
- Rising Rat Populations Linked to Warming Temperatures, Urban Growth, Study Finds
- How Might the 2024 Elections Impact PCOs
- Keeping Track of Termite Identification
- Mosquito Joe Earns EPA's PESP Gold Level Designation
- Texas PestVets Coat Drive Collects Over 850 Items for Soldiers’ Angels
- Conquer Ants Fast!