In my experience, most pest management companies view record keeping as a regulatory burden. This is because most, if not all, states require documentation of:
• Pesticide Usage — Typically this includes the target pest, site of application and types and amounts of products applied. For exterior sites, information on wind speed and direction and the size of the area treated also may be required.
• Wood-Destroying Insect Reports — These reports typically involve completion of the NPCA-1 Form (currently undergoing substantial revision and will become the NPMA-33) or a state-mandated form. Completion of these forms requires reporting evidence of wood destroying insects, damage, determination of previous treatment, recommendation regarding treatment, graphs documenting findings and disclosure of inaccessible areas.
• Termite Treatment Reports — Some states require specific documentation of termite treatments and in many respects this report is analogous to the pesticide usage report. However, these reports typically require documentation of termite activity, damage and treatment.
Most states require that these records be retained for a minimum of two years. I have encountered many pest management professionals who find this burdensome and are chomping at the bit to get rid of these documents. It’s as if getting rid of the records will absolve them of any wrongdoing (I doubt there is much wrongdoing) or relieve them of responsibility regarding claims after the retention period has passed and the records are destroyed.
The most common form of documentation is written reports, but there is a wealth of other information that can prove useful, e.g., photographs, videotapes, moisture readings, etc. In the wood-destroying insect arena new types of detection equipment are being developed: gas detectors, acoustic detectors, infrared photography, x-rays, dogs, ultrasound, etc. Although these technologies expand our capabilities they only are as useful as the person using the equipment, recording the results and interpreting the data.
Hopefully, in this article I can make a strong case for good record keeping and the retention of records as long as practically possible.
REASONS TO KEEP DOCUMENTATION. Documentation plays a major role in the operation of a pest management business. State-mandated record keeping is always subject to inspection. And as a technical director for a mid-sized pest management company, it is something I consider extremely important not only from a regulatory compliance perspective but as a historical record of customer service.
From the state’s point of view, failure to accurately record pesticide applications can result in a violation of state regulations, and in the worst-case scenario, FIFRA. For instance, a technician may inaccurately record the amount of pesticide applied, e.g., final concentration (0.5% instead of the labeled 0.05%) or application to an unlabeled site. This can result in significant fines and potential loss of certification and license.
From a customer’s perspective (more typical of commercial accounts), the service ticket creates a history of service, including units serviced, pest activity, products applied, time and date of service. We occasionally have customers, particularly those not resident at the account, who accuse us of not providing service. Completed service tickets frequently refute such claims.
Over the years, I have had the opportunity to investigate a number of claims. The most frequently encountered and most costly claims involve termite treatment and wood-destroying insect inspections. Remarkably there has been little litigation involving personal injury as a result of misapplication.
As a consultant, the first thing I look for regarding a termite claim is documentation, e.g., inspection reports, graphs and treatment records. With rare exception, claims that had good supporting documentation resulted in more favorable outcomes for the pest management firm or other litigants.
Probably the biggest shortcomings in paperwork are thoroughness and accurate reporting of the findings. A seemingly small error (marking the wrong line on the report) such as reporting the structure had an inaccessible crawlspace, when in fact it had a basement, casts suspicion on the credibility of the entire report. Another major omission is not identifying all of the damage present at the time of the inspection. Typically a few casual x’s are made on the graph to indicate damage, understating the extent of the damage evident at the time of the inspection. If a report is ever used in litigation, it is best to have an accurate baseline to determine the extent of damage since the report was written.
Recording pesticide usage for termiticide applications is another area frequently given little attention. It is important to indicate the area treated, total amount of material applied, final concentration, rate of application (particularly important with variable rate labels), total amount of concentrate used and product name. Don’t forget to retain records for termiticide purchases; they serve to corroborate that enough product is purchased to perform the job as indicated on the service ticket.
BETTER SAFE THAN SORRY. Use all of the tools and documentation you deem appropriate for the job at hand. There is no way to predict how an additional piece of information may help you down the road. Not too long ago we were threatened with a lawsuit from a termite customer who wanted us to buy him a new floor because we failed to protect the home against further termite damage. It was fortuitous that this was an account where we took some digital photographs prior to treatment and made them part of the customer’s file. Once the customer was informed we had pretreatment photographs of the damaged area, the threat disappeared.
Training and quality assurance inspections are the best way of ensuring that technicians know how to properly complete service tickets and inspection reports. Checks of turn-in work and inspection reports will expose paperwork weaknesses that can be corrected through training and, in some cases, individual counseling. It is better to correct these problems before a state inspector or litigation turns up the errors for you.
I’m not suggesting that we take documentation to an extreme; however, it can be your best ally in tough times.
The author is technical director of American Pest Management, Takoma Park, Md. He can be reached at 301/891-2600 or rkramer@pctonline.com.
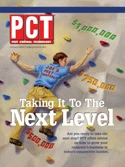
Explore the January 2004 Issue
Check out more from this issue and find your next story to read.
Latest from Pest Control Technology
- Webinar: Maximizing Cash Flow — Key Strategies for Business Growth
- WorkWave Announces Wavelytics
- Rising Rat Populations Linked to Warming Temperatures, Urban Growth, Study Finds
- How Might the 2024 Elections Impact PCOs
- Keeping Track of Termite Identification
- Mosquito Joe Earns EPA's PESP Gold Level Designation
- Texas PestVets Coat Drive Collects Over 850 Items for Soldiers’ Angels
- Conquer Ants Fast!