It may not be apparent yet, but big changes are in store for the termite control industry for 1998 and beyond. New labels that appear on soil-applied termiticides packaged as of Jan. 1, 1998, were designed to, in the words of many, “level the playing field.” Now the question remains: Is it level?
The new labels are considered to be a relative success by the Association of Structural Pest Control Regulatory Officials (ASPCRO) and the National Pest Control Association, which both worked with the EPA to help develop a document calling for the revisions. The ultimate goal of the changes was to create a consistent standard for termiticide labels that would ensure safer handling, use and storage while also maintaining product efficacy.
The resulting new labels, in fact, do address many of these issues and concerns. There are more detailed mixing and treatment instructions, notification requirements, and instructions about personal protection. And while the revisions have also raised some new questions about the practice of termite control, most industry insiders welcome them as long overdue.
“These new changes are nice additions that are only going to help. They are not going to harm anyone,” said Lanier James, president of James Pest Management, Memphis, Tenn., and a member of the NPCA’s Wood Destroying Organism Committee. “They could go even further.” In fact, experts across the industry have similar opinions, and it appears the process of revising termiticide labels is far from over.
SPECIFIC LABEL CHANGES. The document that kicked off the label revisions, the U.S. Environmental Protection Agency’s Pesticide Regulation (PR) Notice 96-7, went into effect at the start of 1998. More than 10 years in the making, the notice called for manufacturers to revise their labels so as to incorporate standardized language about handling, use and safety precautions that would help reduce risk while also maintaining efficacy. The NPCA was instrumental in the development process by providing suggestions and recommendations to the EPA. “Where I think we played a prominent and proactive role,” said Bob Rosenberg, NPCA director of government affairs, “was in trying to form a broad industry consensus in what had been fairly contentious issues.”
Originally, the labels were to be revised as of Oct. 1, 1997, but because of excess stocks, the EPA in September granted manufacturers a three-month extension. Distributors still have until Oct. 1, 1999, to distribute any old-label product. Meanwhile, PCOs have no such deadline for applying existing stocks of old-label product.
Considering the extension, it’s likely the labeling changes won’t have an effect on PCOs until late this year or early in 1999. That’s when, experts say, most of the supplies of the currently labeled products will be depleted, and PCOs will begin using termiticides that carry the new labels. “We’re hearing that about 85% of the old-label product will be gone in the first year,” said Jim Wright, chairman of the ASPCRO Termiticide Label Review Committee and regulatory supervisor for South Carolina’s Department of Pesticide Regulation. “Then it will take several years beyond that to cycle through the remaining 15%.” The standardized language on the new labels provides many specific instructions for PCOs, regardless of which product they use. For instance, the new labels prohibit the use of less-than-label rate for termite pretreats. Post-construction application rates remain at the discretion of the PCO, unless state law requires label rates. Labels also prohibit PCOs from retreating structures on an annual basis unless clear evidence of an infestation or breakdown of the termiticide barrier exists. In another interesting change, labels now bear instructions regarding the personal protective equipment (PPE) requirements for termiticide handlers and applicators. These PPE requirements spell out the type of protective gear that must be worn when handling and applying termiticides. The requirements vary based on the toxicity category of the product. For example, applicators using termiticides marked with a “CAUTION” label must wear a long-sleeved shirt, long pants, socks, shoes, and chemical-resistant gloves. They must also wear protective eyewear when rodding or performing a sub-slab injection. The label also spells out mixing instructions for the products, including foams. Regarding treatments, the labels now provide specific instructions relative to construction areas. The PCO still must treat vertical barriers at 4 gallons/10 linear feet per foot of depth, to the top of the footing, however PCOs no longer have to treat below the depth of four feet. For postconstruction treatments, the applicator has to treat to the top of the footing or to a minimum depth of four feet, whichever is less. This has to be accomplished by trenching the soil and rodding the bottom of the trench. Previously, labels didn’t require both trenching and rodding. Applicators will also have to trench and rod into the trench along the foundation in crawlspaces. In addition, the labels contain a host of other requirements, including detailed mixing instructions, what to do in the event of a leak, the notification of contractors in advance of termite treatments, and the plugging of all drill holes after treatments. EARLY QUESTIONS. The biggest concerns raised by PCOs and industry experts have to do with the new PPE requirements, the requirement to trench as well as rod, and, for some PCOs, the requirement to use the label rate on pretreats. “Those are probably the most visible changes and the most likely to be questioned,” said James. “These are ‘new’ old areas that are being exposed, and they are going to be questioned.” Despite the fact that the wording on the new labels was supposed to be standardized, some of the labels differ on the points of personal protective equipment requirements. Bayer Corporation, for instance, worked closely with ASPCRO in getting the new label for its Premise termiticide completed. Interestingly, the new Premise label contains one difference from other termiticide labels: applicators do not need to wear a respirator when applying the product in confined spaces. “We have developed quite a case of justification for the fact that Premise doesn’t get into the air in a detectable level,” explained Gregg Storey, Premise product manager. “If you can’t detect it in the air, there’s really no reason for wearing a respirator, and both EPA and ASPCRO agreed with that.” The company submitted the results of laboratory and indoor air monitoring studies to make its case. Wright points out that inconsistencies in label wording were to be expected. “We anticipated that this was probably going to happen,” Wright said. “The PR Notice clearly gives the registrants the latitude to submit the toxicity data on their particular molecules that will support the lesser PPE requirements on the end use solution.” Furthermore, Wright said, a manufacturer may very well be justified in presenting a case for less strict PPE requirements for their product. Another reason for differences between product label wording has to do with the way the pesticide registration process works, Rosenberg explained. “Each product label is reviewed by and approved by a different team at EPA,” he said, “and sometimes what that leads to is discrepancies from one label to another.” And says Richard Kramer, president of the consulting firm Innovative Pest Management, Olney, Md., differences in PPE requirements for soil-applied termiticides should not play a major role in the PCO’s buying decision. “There are so many other criteria to determine what type of product to use,” he said. Instead, he adds, PCOs should consider such factors as the demonstrated efficacy and longevity of a given product in a specific geographic area. Wright said the association’s primary concerns with regard to PPE differences are that the requirements are appropriate relative to the potential exposure to the applicator, and the requirements are worded in such a way that they are enforceable. “For example, if the requirement is to wear goggles and long-sleeved coveralls,” Wright explained, “then we prefer that the label say the applicator must wear those things, as opposed to ‘should’ or ‘recommended.’” In his opinion, says James, the PPE requirements may not go far enough. “There needs to be more research conducted in the type of clothing that needs to be worn,” he said. For instance, if rubber gloves and boots are required, then why shouldn’t applicators be required to wear rubber coveralls as well, he questions. The requirement that PCOs trench as well as rod for most construction types will likely cause a few headaches for pest control companies as they re-organize their services to incorporate the additional work and time needed to conform. But most experts say rodding plus trenching should both be performed. “That is something the industry has recommended for years to better establish a continuous barrier,” Kramer said. Mike Potter, extension entomologist at the University of Kentucky, agrees. “It’s a lot of work to trench,” he said, “but research has shown that you really ought to trench in conjunction with rodding in order to get good, uniform coverage.” And one of the biggest questions raised by the new labels concerns ventilation. The label requires that when using termiticides characterized by the signal words “WARNING” or “CAUTION,” that handlers wear respiratory protection when applying the material in a non-ventilated space. But the notice fails to define what is meant by “non-ventilated,” and the resulting definitions from around the industry appear to vary. ASPCRO’s Jim Wright points out that, in general, most crawlspaces are not going to be well ventilated. “Proper ventilation for a structure and for inhalation purposes are two completely different things,” Wright said. “I would think that a crawlspace is clearly not well ventilated. On the other hand, if you’re drilling a slab in a post-construction treatment, such as a basement, that’s a different circumstance.” Industry consultant George Rambo points out that pest control operators may want to check with their local regulatory officials to determine if they have set guidelines pertaining to ventilation in that state. Kramer adds that it may be most appropriate for PCOs to use their own judgment to determine if a crawlspace is ventilated. “The company should develop a policy statement regarding how they define an unventilated crawlspace,” he said. “They should tell their technicians to use that criteria to determine if a crawlspace is ventilated or not.” PRACTICAL APPLICATION. The instructions on the new labels may take some time to hit home for PCOs, and most experts are recommending that PCOs prepare to follow them and know where to go for clarification when questions arise. “I’m sure there are things on the new labels people are going to be unclear about,” said Rosenberg. “That’s where it’s going to be essential for PCOs in every state to work with their regulatory officials.” Rosenberg said there is concern that having two sets of labels circulating in the market — the old labels along with the new ones — will create some competitive disadvantages among PCOs, but any discrepancies should quickly diminish. “We’re working with the regulatory community to make sure there is a smooth transition to the new labels,” he explained. He added that some PCOs may be tempted to use the old labels for as long as possible, considering the fact that the new labels are more expensive to comply with, considering the additional time and materials necessary. “We know there are PCOs who think the old label is preferable to the new label,” Rosenberg said, “but they would be making a very serious mistake to buy a lot of old label product on the presumption that they will forever be able to use old product.” Doing that, Rosenberg said, might only open PCOs up to other sorts of inquiries, including those relating to consumer fraud. And industry insiders say it’s important to keep in mind that discrepancies on various product labels are also likely attempts by manufacturers to give their products a strategic advantage in the marketplace. Rosenberg points out the while differences between product labels may still exist, they are much less significant than in the past. “It used to be that people made buy-sell decisions based on a lot of things,” he said, one of which was which label they liked the best. “One of the things we’ve tried to do is take that out of the purchasing mix,” he added. “It’s not completely out but it’s less a part of the process than it was before the PR Notice.” Considering the label changes originally proposed by the EPA in 1994, Rosenberg adds, the final PR notice is a definite step in the right direction. “I think for the most part the final PR notice was probably a very good public policy initiative based on a whole series of compromises.” Although the new labels were due out with the new year, it’s likely the process of revising and updating them will be an ongoing process. For instance, already the EPA has, at NPCA’s request, asked manufacturers to again revise the wording with regard to precipitation and runoff. (Application will be prohibited if there is a chance of runoff.) And other issues, such as ventilation, PPE requirements, and determining the necessity of retreats will likely be questioned by PCOs in the coming months. Until then, Wright recommends, PCOs should work to understand the labels completely. “If they have any questions, PCOs should know they have two very good resources,” he said. “The first is the manufacturer, and the second is their state regulatory agent.” The author is managing editor of PCT.
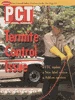
Explore the February 1998 Issue
Check out more from this issue and find your next story to read.
Latest from Pest Control Technology
- Envu Announces Lichtenstein as Chairman of Board of Directors
- Spider Expertise, Cockroach Species, AI Tools for Disease Transmission Hot Topics at Purdue Conference
- Rose Pest Solution Promotes Kandler to District Manager of Columbus (OH) Office
- Webinar: Maximizing Cash Flow — Key Strategies for Business Growth
- WorkWave Announces Wavelytics
- Rising Rat Populations Linked to Warming Temperatures, Urban Growth, Study Finds
- How Might the 2024 Elections Impact PCOs
- Keeping Track of Termite Identification