
As pest control professionals, we rely on our equipment every day to help us provide our customers with quality service. Well-functioning pest control equipment is critical to our personal and company success.
Here are some tips to help you take care of your equipment. Most of these tips have come from many years of observing pest control equipment misuse, abuse, failure and indifference. A little extra attention toward your equipment will pay big dividends in the form of reduced downtime, lower repair bills, longer equipment life and fewer canceled appointments.
RIGHT EQUIPMENT. The first step in taking care of your equipment is starting with the right equipment. The equipment you purchase will have a huge impact on how well it works for you and how long it lasts.
Here are some key points to keep in mind when purchasing equipment:
- Professionals should buy quality equipment. Cheap stuff doesn’t last and the problems it causes will cost you a lot more in the long run.
- Little stuff matters. When it comes to power sprayers, many buyers look at the big stuff (engine, pump, reel, etc.) and ignore small things like plumbing fittings and valves. A broken plastic fitting that causes a chemical spill will suddenly become very important.
- Are replacement parts readily available? If not, the downtime you experience waiting for parts will be financially painful...and stressful.
- Is the equipment easy to service and repair? Who will do the repairs?

Ask and answer these questions before writing a check to purchase equipment.
Another key point for companies with multiple technicians and vehicles is standardization. Pest control equipment standardization reduces all kinds of complexities and problems. Training, use, maintenance and repair parts inventory are all much easier when there is only one brand/model of a particular type of equipment to worry about.
SMART USE IS CRITICAL. This sounds obvious, but like common sense, smart use of pest control equipment is less than universal. Here are some general guidelines to follow:
- Technicians need to report equipment problems promptly. Too many technicians will live with equipment problems with a stiff-upper-lip strategy that costs the company more in the long run.
- Fix small problems promptly. Small problems are fast and cheap to fix. Left unchecked, small problems always become big problems. Big problems take longer and cost more to fix. Worse, they usually occur during your busy season, when the impact is greatest.
- Periodic calibration is essential to good results. Recalibrate regularly or when conditions change.

HELPFUL TIPS. Here are some specific equipment strategies that pay big dividends:
- Check/clean sprayer filters regularly.
- Clean spray tips regularly to ensure a good, even pattern and proper application. Use a gentle detergent and a soft-bristled brush. Do not use pins, knives or anything else metal, which will damage tips.
- Change sprayer tips annually. Tips wear out, which means higher chemical costs. It is much cheaper to buy a new tip than to allow your chemical costs to go up.
- Clean out your equipment regularly to prevent residue build up; clogged lines, fittings and spray tips; and lots of other undesirable problems.
- Don’t overpressure equipment. It will reduce equipment life.
- Release the pressure on your equipment after each stop. It will extend equipment life.
- Before driving off, check to ensure your equipment is secure. A lot of equipment damage comes when equipment is bouncing around the vehicle. Further, ensure equipment will be secure in the event of an emergency (hard braking, swerving, accident, etc.).
- Avoid freeze damage. This was the subject of a PCT article in October 2016 titled “Wild Winter.”
PREVENTION IS KEY. Preventive maintenance is an area where we see the most room for improvement. Too many pest control professionals fix their equipment when it fails, rather than anticipating problems and doing regular preventive maintenance.
Here is a universal truth that your company will face: Your pest control equipment eventually will need service.
Either you can decide when to do the service or you can let the equipment decide. If the equipment decides, you can bet it will be during your busiest time when you are using it the hardest and when you will be waiting in line for repairs behind everyone else who didn’t do their preventive maintenance.
If you decide, you can service the equipment when it is convenient for you, when the impact on your business will be minimal.

Don’t wait for problems. Do your preventive maintenance. If you don’t have a preventive maintenance program, or don’t know what to do, contact your equipment provider.
SUMMARY. No one ever has time to anticipate and prevent problems, though everyone seems to have time to fix equipment that has stopped working. A small reallocation of this approach, including selecting the right equipment, training technicians, anticipating/preventing problems, and performing preventive maintenance will make your life easier and your wallet a little fatter.
All photos courtesy Andrew Greess.
Andrew Greess is president of Qspray.com, a pest control equipment website. He is author of “Stop Spraying Money Down the Drain” and the soon to be published, “Ultimate Guide to Reducing the Risk in Your Pest Control Business.”
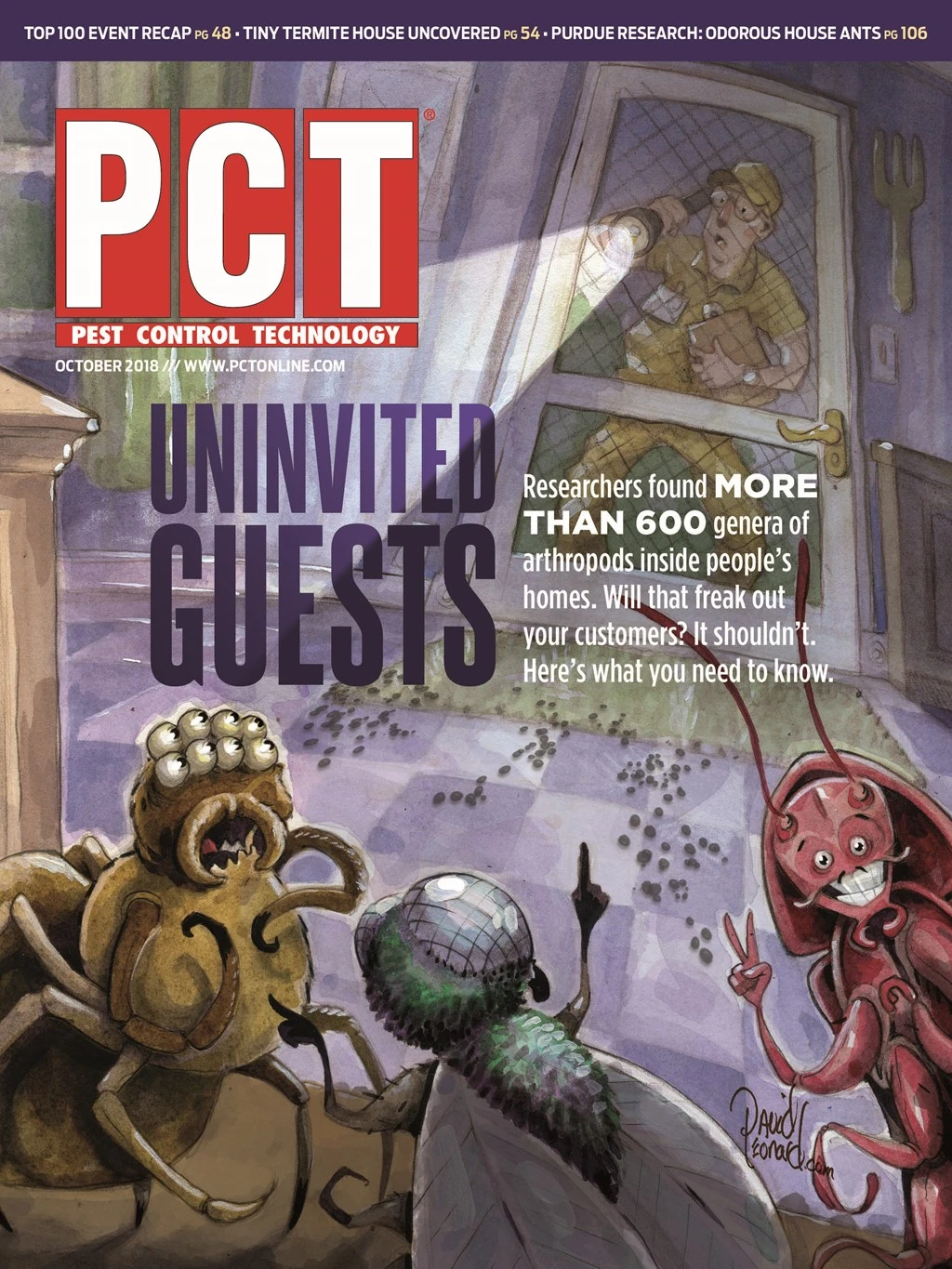
Explore the October 2018 Issue
Check out more from this issue and find your next story to read.
Latest from Pest Control Technology
- Understanding Rodents and Bird Flu
- Green Pest Solutions Awards Safest Driver New 2025 Ford F150
- UF/IFAS Sheds Light on Tiny Invaders During Termite Awareness Week
- Registration Open for Lawn & Landscape Technology Conference
- Fleetio Launches Automotive Service Excellence Scholarship
- WorkWave Appoints John Phelan as CTO
- PMPs Use Capitol Hill Visits to Push for Preemption
- 20 Trapping Tips