Eliminating and controlling pests within and around food-handling plants and warehouses can be challenging. Incoming raw ingredients and thousands of different types of supplies will introduce pests to food-processing plants, while food odors, moisture and heat as by-products of food production also serve to constantly attract insects, rodents and birds to the facility or structure.
Moreover, commercial food plants are usually brightly lit at night, attracting still more flying and crawling insects. To combat this pest pressure, food plants must incorporate unrelenting quality assurance programs that combine good manufacturing practices (GMPs) with effective and progressive pest management operations.
Used in a broad context, Integrated Pest Management (IPM) programs involve the integration of both nonchemical and chemical tools and techniques for managing pests. For food plant IPM programs, the emphasis is especially placed on the nonchemical practices of pest exclusion and plant sanitation programs because these efforts produce the best long-term and cost-effective results. Pesticides and trapping programs are used for controlling or eliminating those pests that, despite nonchemical efforts, have managed to enter and exist within or around the plant.
HACCP, GMPs and IPM. Over the past several years, there has been renewed interest in the Hazard Analysis Critical Control Point (HACCP) concept — especially as it relates overall to pest management. The HACCP concept was first developed by the food industry during the 1960s. Presently, there are government mandates requiring HACCP programs for certain food manufacturers, such as meat and poultry, fruit juice and seafood.
HACCP uses science and common sense to prevent biological, chemical and or physical hazards from occurring in our food production. One of the key elements to keep in mind is that HACCP is a preventive, not reactive, system. It is based on the concept of identifying hazards that are likely to occur and then determining the preventive measures for the specific hazards.
Prior to the implementation of a HACCP program, good manufacturing practices, (GMPs) and Standard Sanitation Operating Practices (SSOPs) must be in place. GMPs are the criteria as set forth by the Federal Drug Administration for food manufacturers to ensure their food is free from adulteration. Sanitation and pest management programs are included as two critical parts of the GMP program. Specific guidelines for how a plant shall be kept clean are outlined within the SSOPs. Thus, HACCP, GMPs, SSOPs and IPM are all basically related to one another and together they share the same goal: to create a safe and sanitary environment that minimizes the risk of a food safety hazard occurring.
The following are guidelines for implementing an IPM program at a food plant.
PEST INSPECTIONS. Pest management inspections are intended to discover anything that might cause or permit contamination or adulteration of food items by pests. All areas of the plant including incoming raw ingredients, finished product, and interior and exterior areas must be regularly inspected. Skill and on-the-job experience are required to conduct insightful inspections. Nevertheless, here are a few inspection tips that can help to locate potential pest problems:
• Identify those areas of the plant that are most difficult to access for cleaning. Interview the sanitation staff to find these areas then target them for pest activity. Obviously, when an area is difficult to clean, food residues and various types of clutter tend to accumulate and as such, pests proliferate in these areas. It is common for 80 percent of persistent insect problems to originate within 20 percent of the plant. And, the 20 percent is usually an area difficult to access or clean.
• Identify areas of recent or previous processing equipment malfunctions. Such malfunctions usually result in food accumulating in various nooks and crannies and structural voids of buildings and equipment. Often, in an effort to get the plant up and going again, these areas are not cleaned as thoroughly as they should be and serve as pest eruption points.
• Always inspect any previously infested areas. The saying “pests re-infest” is true. Often pests repeatedly seek out the same harborages and microenvironments because they provide ideal cover, temperature, moisture or food. Maintain a history of the locations of all pest problems and re-inspect these areas regularly.
MONITORING PROGRAMS. Pest monitoring efforts play a critical role in an IPM program. Monitoring programs help to detect newly introduced pests, identify pests and pinpoint the location of infestations. There are two types of monitoring programs: general pest monitoring and pheromone trap monitoring for stored product pests.
General Pest Monitoring. General pest monitoring is accomplished using various types of sticky traps designed to simply capture any insects that crawl or land on the sticky surfaces. Monitoring traps come in all shapes and models. Installing a monitoring trap can be as simple as placing a few folded sticky traps in areas you wish to check insect activity. Monitors can also be installed within protective boxes. When installing general pest monitoring traps consider the following:
• Place monitoring traps in areas subject to pest activity such as near entryways, clutter or processing equipment.
• Create a schematic of the plant showing placement of the monitoring traps. Number and date each trap and record the results for the trapping program. An analysis of monitoring results will help accurately pinpoint areas of infestation.
• ILTs also serve as valuable monitoring tools for various flying insects.
Pheromone Traps. For food plants that handle or process grains, pheromone traps are available for important stored product pests. Species-specific pheromone traps are not available for all stored product pests, but new pheromones and traps are constantly being developed.To obtain maximal information from pheromone traps, they must be installed and used correctly.
• For general monitoring programs, pheromone traps are usually installed at about rates of one trap per 30,000 to 100,000 cubic feet. The shorter distances are used for those plants under high pest pressure or plants wanting to maximize efforts in preventing pest outbreaks. However, to “zero-in” on possible infestation sites or for mass trapping programs, traps can be installed at rates of one trap per 3,000 to 10,000 cubic feet.
• Pheromone traps are typically installed in a grid throughout plants using perimeter walls and interior pole supports. Traps are typically spaced at 25 to 50 feet intervals, but spacing can vary depending on airflow patterns, room layouts and tolerance levels.
• Good locations for pheromone trap placements include areas that collect food debris. Hard-to-reach areas around equipment, near conveyors, ledges, closed storage areas, utility and enclosed conduit junction boxes and motor boxes are all excellent monitoring sites.
• Detailed record keeping and a plant map illustrating the locations of all pheromone traps will provide the best return for the time and money spent on the pheromone-trapping program. Records should indicate the trap location, trap number and the number of insects captured for each period. Data can then be analyzed according to monthly, quarterly and annual trends and pest management decisions can be made accordingly.
EXCLUSION PROGRAMS. Completely denying all pests entry to a commercial food plant is not easily attainable or even possible. A more realistic goal is to keep the numbers of pests entering the plant daily as low as possible. This can only be achieved by constantly striving towards a tight plant.
• A tight plant can be accomplished by regularly inspecting and repairing the plant and being relentless in encouraging employees to keep entryways closed.
• Doors that are improperly fitted, warped, broken or unscreened will provide easy access to pests. Door repair and closure programs must be ongoing and considered high priority by management.
• Plant-wide pest denial educational programs should be emphasized by plant management and cooperation of employees in keeping all entry ways closed when not in use should be encouraged. This is easier said than done, but periodic employee meetings stressing this objective are helpful — and do work.
SANITATION AND GMPS. Pests must have resources to survive. These resources include the obvious: food, water and shelter. Of course, it is a challenge to eliminate these resources from a food plant on a large scale. But most pests require protected, isolated areas and “microhabitats” to develop. If we can identify, control and eliminate the pest’s resources from these areas via “micro-sanitation,” we can significantly limit or eliminate pest populations entirely. In fact, it is true that sanitation is pest control.
Exterior Sanitation Considerations. Exterior sanitation programs are vitally important in the long-term management of pests around food plants. Weedy areas and fields outside the plant may be the source of continual mouse or insect infestations that disperse into the plant. Remember the following tips when designing your exterior sanitation program:
• Lawns surrounding food plants must be cut regularly and weeds and other uncontrolled plant growth must not be permitted close to the plant exterior walls.
• Trees and shrubbery should be planted at distances of about 30 feet away from the buildings. A vegetation-free, gravel perimeter 30 to 36 inches wide around the buildings will discourage rodent and insect activity, as well as serve as an inspection pathway and area for installation of bait stations or other rodent control devices.
• Any type of exterior debris, such as trash piles, empty containers, old machinery and construction materials, must not be allowed to accumulate because such clutter is highly attractive harborage sites to rodents, wildlife and insects.
• Properly drain water off of roofs and away from building foundations. Accumulating water that remains for prolonged periods is a vital resource for flies, ants, rodents, birds and wildlife and will attract pests to the grounds regularly.
Interior Sanitation Considerations. Note the following:
• Extremely thorough cleaning practices must be implemented to eliminate the food resources for insects, especially when we consider the tiny size of the larvae of many of the stored product pests (e.g., saw-toothed grain beetles, Indian meal moths, etc.).
• The various small nooks, crannies and internal voids within processing equipment and utility lines are often the culprits behind many persistent and recurring pest problems. These areas must be constantly inspected, disassembled and cleaned to remove accumulating food.
• All overhead areas, such as utility lines, walls, windows, ceilings, structural beams, conduit, etc., must also be kept free of product residues. Pest populations can explode in these hard-to-reach areas if they are not cleaned regularly.
The Perimeter Inspection Aisle. One of the most important pest management and sanitation practices in food plants is the maintenance of inspection aisles or perimeter strips. The inspection aisle is that area which separates stored product from wall areas and/or the area between rows of stored pallets of product. This space permits thorough product and building inspections to be conducted between the walls and product and between rows of stacked products.
Inspection aisles also provide the space needed to remove spills, repair damaged walls and equipment, install rodent traps and apply any pesticides. Perimeter wall inspection aisles should be painted white and adequately lighted from above. A good inspection aisle allows for spaces of 18 to 24 inches between product and wall areas.
NONCHEMICAL MANAGEMENT. Many food plant pests can be effectively managed via nonchemical programs. Or, nonchemical programs can be used as important supplements to chemical pest management programs.
Rodent Control. Rodent management programs in the food industry are traditionally comprised of a three-tier protection system.
• Tier One — place exterior rodenticide bait or trap stations along the property fence row. All bait stations should meet EPA tamper-resistant criteria and must be secured to the ground, fence or heavy, low-profile concrete block (e.g., 16 by 16 by 1 inch).
• Tier Two — line bait or trap stations along the plant’s entire exterior perimeter wall.
• Tier Three — use multiple catch mouse traps located along the interior perimeter walls of the facility or structure. These traps can be spaced at 20 to 40 feet intervals, as well as flanking all entryways. The shorter placement intervals are used when maximal protection is desired or in areas of high mouse pressure. Also, mouse traps should be positioned nearby any areas that have structural defects that might allow rodents into the plant (gaps around utility lines, improper fitting doors, etc.).
• Record keeping and keeping traps clean and in good repair are also essential.
Insect Light Traps. Insect light traps (ILTs) provide an important nonchemical role in flying insect control programs. ILTs also provide valuable monitoring data about the number and kinds of flying insects entering or present within a facility, including grain pests. ILTs work continuously and attract many different types of flies and stored product pests.
• Insect light traps should be located in those areas of maximum fly activity — referred to as flyways. Flies are attracted to the inside of plants from the odors and warmth from windows or doors. Thus, entryways are key locations for ILTs.
• Usually light traps are placed within 12 to 15 feet inside a door and in a location or position that will not allow the ultraviolet light to be visible from the outside. This will prevent attracting insects into the building.
• ILTs should be evenly spaced at about 50-foot intervals throughout the suspected flyways. Space traps closer together for heavy infestations.
• The most effective height installment for filth flies that spend most of their time cruising low to the floor, is between 3 to 5 feet off the floor.
• Bulbs should be changed at least once a year. In the temperate regions of the U.S., April 1 is a good time to change out bulbs to coordinate maximum bulb strength with the greatest fly activity. In the South, many food plants install new bulbs every six months.
RECORD KEEPING. Every food plant IPM program requires effective record keeping. Detailed reports should accompany inspections. There is no one perfect style for inspection reports. Many companies use common check-box style reports. Some inspectors prefer to write descriptive reports and supplement the report with check box reports to ensure nothing is overlooked.
Regardless of the form or style, it is important that the report lists any deficiencies and is circulated among the proper personnel for attention (usually corrective action reports are filed as part of the inspection process).
• Another essential record-keeping practice involves recording the locations of all pest monitors, mouse traps and exterior bait stations within or around the plant. All devices should be recorded on plot diagrams with their appropriate numbers. Some plants use different symbols or colors to represent each type of device.
• The numbers of insect captures and the types of insects should also be recorded. In this way, trends, which indicate increases in a particular pest population, can be calculated on a regular basis. Trap numbers and pest data should be carefully summarized on a monthly, quarterly and annual basis. In this manner, decisions can be proactively made regarding the necessity of using pesticides, additional cleaning, increasing pest denial programs, repairing walls, etc.
It is important to note that without good records, we keep ourselves in the dark as to whether or not a pest problem exists or may be increasing. We often compensate for this lack of insight by over-applying pesticides, “just to be safe.” Get the most out of your IPM program — keep good records.
SUMMARY. IPM programs for the food industry should be based on a solid foundation of GMPs, with emphasis on sanitation, pest proofing and structured monitoring and inspection programs. Pest reduction programs, pesticide choices, application procedures and pesticide frequency should be tailored to inspection and monitoring data results.
The author is an urban and industrial entomologist and rodent control specialist who can be reached via e-mail at bcorrigan@pctonline.com.
ONLINE ONLY: CHEMICAL AND PESTICIDAL FOOD PLANT PROGRAMS
Insecticides and other pesticides comprise an important part of an IPM program. In fact, due to the nature of food manufacturing and the intense amount of pest pressure on food plants, it is often impossible to eliminate pests without the use of quality insecticides and professional applications. Application equipment is also a critical component to effective pesticidal applications inside food plants. At certain times and for certain locations, insecticide applications inside food plants must be directed into specific habitats where insects may be hiding. Commonly this is in cracks and crevices or inside equipment, wall voids or in various hard-to-reach areas. Warehouses may require effective and powerful space treatments (ULD or “fogging”). Pesticide applications in food plants can be categorized into two broad types of applications: residuals and non-residual applications. Both types are essential components of food plant IPM programs. Non-residual applications are those such as the use of pyrethrums to flush out insects hiding in a piece of manufacturing equipment or the use of ultra low dose treatment (ULD) to treat for flying insects in a portion of the warehouse. In both cases, the killing effect of the pesticide only last during the actual time of treatment and there is no pesticide killing residual left over. On the other hand, residual pesticidal treatments are those that may last for days, weeks or months depending on the formulation applied. Examples of residual pesticide applications used in food plants include ant and cockroach baits, dusts and various active ingredients such as cyfluthrin applied as pressurized liquid applications. Following are a few common examples of typical residual and non-residual applications used for food plant pest management. Residual Exterior Treatments: · Use a residual perimeter insecticide along exterior and interior walls during the peak insect activity months of the spring and summer to help suppress insect populations and their ingress into plants. This powerful residual insecticide will eliminate the need to re-spray the same perimeter areas weekly, will save on labor input, as well as minimize the amount of pesticide applied to the plant’s exterior. · Treat expansion joints at the foundation wall and exterior slab (low pressures of 15 psi or less, using a pin stream nozzle opening directed into the expansion joint). This type of application takes longer to conduct than a higher-pressure fan treatment of the foundation wall — ground junction area (i.e., a “band treatment”), but offers greater pest elimination. · For ant control, new baits are available which are highly effective for many ant species common to warehouses and food plants built on large slabs. Baiting is most effective when ant infestations are located and entryways identified. Applying bait directly to foraging trails will increase the acceptance of the bait and allow for colony elimination. · Baiting programs for fire ants must be carefully planned and well-implemented taking into consideration the local weather conditions. Unfortunately, fire ant control in the food industry is sometimes delegated to lawn maintenance crews whom simply treat mounds by pouring insecticide “drench” or dust treatments onto the visible mounds as the mounds become large. These types of treatments result in merely “harvesting” fire ants over the long term instead of eliminating or significantly suppressing the fire ant colonies. Fire ant treatments are most effective using a broadcast application in the infested areas. Monitoring is essential to determine ant pressure and re-application. Interior Non-Residual Applications: Non-residual pesticide applications are the most common method of applying pesticides inside food plants. 1. ULD Space Treatments (Fogging). Space treatments of food plants (also known as “fogging”) can be a useful supplement to total pest management programs. Space treatments are used to knock down flies and various flying and exposed crawling stored product pests at certain times of the year. · The Prescription Treatment ® brand ultra low dose BP line of pyrethrins and piperonyl butoxide formulations offer outstanding options for space treatments. BP-50, BP-100 or BP-300 contact insecticides can be used at the rate needed for the particular situation. Moreover, these insecticides can be used in a wide variety of ULD® application equipment. · For food plant pest management programs, getting the insecticides directly into the insects harborages is a critical component to successful pest elimination. For this reason, deep harborage treatment equipment such as the Micro-Injector ® provides an essential piece of equipment in the overall program. · It must be emphasized that space treatments are most effective when they are applied in a directed manner into inaccessible structural or equipment voids or directed towards fines collecting on hard-to-reach or inaccessible ledges within plants until these areas can be properly cleaned and the breeding sources eliminated. · For general space treatments of large open areas or for warehouse “foggings” to knock down flying insects, the use of Whitmire Mirco-Gen’s heavy duty ULD ® cold aerosol commercial-level foggers such as the G-77 are best suited to these large jobs. 2. Flushing. Many times small pockets of insects (cockroaches, various stored product pests) are discovered upon routine inspections within equipment or structural nooks and crannies. In these cases, use non-residual flushing and killing agents. a. Interior Residual. Following a flushing program, these areas can either be sealed or treated with approved residual products such as Perma-Dust or Tri-Die. These residual pesticides offer outstanding longevity, combined with low toxicity and are perfect choices for food plant IPM programs when Crack and Crevice ® applications are required. Interior residual treatments for food plants generally consist of spot and Crack and Crevice ® applications of various formulations of insecticides. Two pests in particular, ants and cockroaches, must be carefully kept in check. · Ants in food plants can be eliminated via the use of liquids, dusts or baits. Over the past several years, baiting programs for both exterior and interior areas using the Whitmire Micro-Gen Advance ™ ant product line has proven very effective. · For indoor areas, Advance ™ Dual Choice ® ant bait stations installed in areas of ant activity allows for worker ants to take the baits back and share it with the colony to achieve elimination. · Cockroaches can be eliminated with the use of Whitmire Micro-Gen’s Avert ® cockroach baits or bait stations. Avert® Cockroach Bait Stations are labeled for use in virtually all food areas of food plants. Avert ® gels are permitted as Crack and Crevice ® treatments only in areas of food plants as specified on labels. When combined with good inspections to locate the harborage areas of the cockroaches, Avert ® cockroach baits provide outstanding, long-term cockroach elimination and protection. |
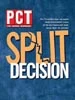
Explore the July 2002 Issue
Check out more from this issue and find your next story to read.
Latest from Pest Control Technology
- Rose Pest Solutions Becomes Official Pest Provider of Chicago Fire FC
- WSPMA Hosts Legislative Day at Washington State Capitol
- A-1 Pest Control Marks 59 years in Business
- Hawaii PCO Shares Regulatory Challenges, Business Impacts from Lahaina Wildfires
- 5 Tips for Reducing Waste in the Office and in the Field
- OvoControl Now Available in Chile
- Envu Announces Savings Programs for Pest Management Professionals
- Follow the Trail